Why Pipeline Welding Inspection is Important for Long-Term Pipeline Security
Why Pipeline Welding Inspection is Important for Long-Term Pipeline Security
Blog Article
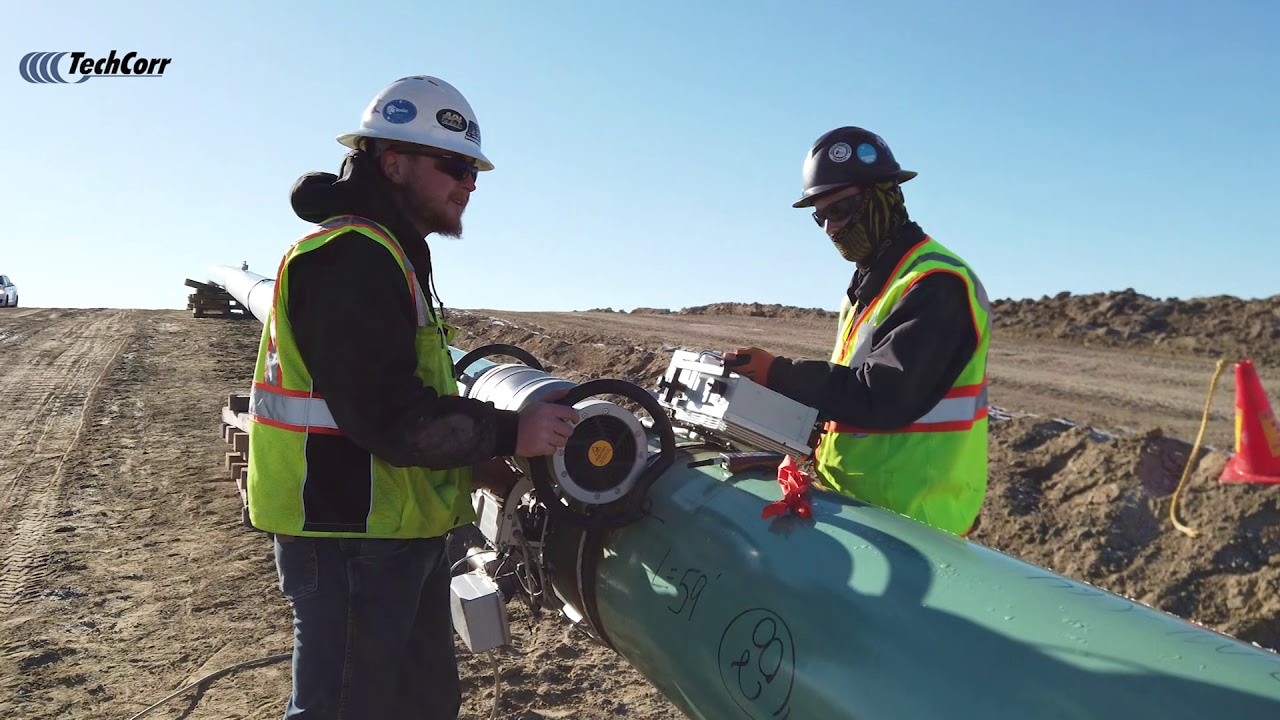
Ideal Practices for Pipe Welding Inspection: Methods, Criteria, and Treatments to Attain High Quality Guarantee and Conformity
Effective pipe welding examination is crucial for making certain the integrity and safety and security of crucial framework. Understanding the complexities involved in each stage of evaluation is essential to achieving compliance and reliability in pipeline systems.
Importance of Welding Inspection
The integrity of bonded joints is paramount in making sure the security and dependability of pipe systems. Proper welding strategies and complete assessment procedures are important to avoid failures that can result in disastrous cases, environmental damages, and loss of life. Pipeline Welding Inspection. Welding assessment works as a preventative action, identifying issues such as splits, porosity, and insufficient fusion before they rise right into serious concerns
Additionally, pipeline systems frequently run under high stress and severe problems, making the top quality of welds even extra essential. Regulatory compliance is an additional significant element, as different criteria determine the quality control procedures that should be abided by in pipeline building and upkeep. Failing to abide can cause lawful ramifications and economic losses.

The duty of welding assessment prolongs past mere confirmation of craftsmanship; it includes the guarantee of lasting operational stability. This includes a methodical technique that includes not only visual inspections yet also advanced non-destructive screening methods. Ultimately, effective welding evaluation is a financial investment in the long life and safety of pipe systems, ensuring they work as meant while lessening risks linked with material shortages.
Secret Examination Techniques
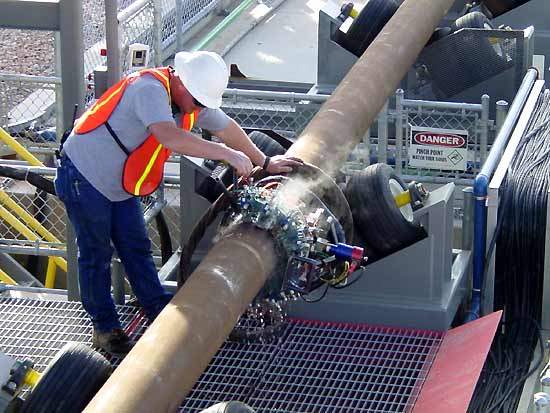
Aesthetic examination, frequently the first line of protection, permits the recognition of surface defects such as fractures, undercuts, and porosity. Ultrasonic testing utilizes high-frequency acoustic waves to find internal defects, supplying a comprehensive assessment of weld honesty. This non-destructive approach is specifically reliable for identifying gaps that may not be visible externally.
Radiographic screening involves using X-rays or gamma rays to create photos of the bonded joint, disclosing interior issues. This strategy offers comprehensive insights however might need specialized equipment and safety and security considerations. Last but not least, magnetic particle screening is reliable for spotting surface and near-surface stoppages in ferromagnetic products, using magnetic fields and fine iron particles.
Sector Standards and Regulations
Conformity with industry requirements and regulations is crucial for making certain the high quality and safety and security of pipe welding evaluations. These criteria offer a framework for finest practices in welding procedures, products, and evaluation techniques, permitting organizations to reduce defects and enhance the integrity of pipeline systems. Trick bodies such as the American Culture of Mechanical Engineers (ASME), the American Welding Society (AWS), and the International Company for Standardization (ISO) state standards that are extensively recognized and taken on within the industry.
In the United States, guidelines from the Pipe and Hazardous Materials Safety Management (PHMSA) control the security of pipe operations, mandating rigorous assessment methods. These standards not only serve to safeguard public safety and the atmosphere but also make certain compliance with contractual and legal obligations. Adherence to the pertinent codes, such as ASME B31.3 for process piping, is crucial for keeping operational performance and governing compliance.
Additionally, continuous updates and revisions to these criteria mirror technological developments and developing sector methods, emphasizing the need for organizations to remain informed and train employees appropriately. Eventually, durable compliance with well-known requirements cultivates trust fund and dependability in pipe framework, protecting both properties and stakeholders.
Reliable Assessment Procedures
Efficient assessment procedures are critical for recognizing possible issues in pipe welds and making certain the total integrity of the system. A methodical approach to evaluation encompasses a number of key stages, including pre-weld, in-process, learn this here now and post-weld assessments. Each stage plays a vital duty in maintaining quality control.
Throughout pre-weld assessment, it is important to evaluate the products and joint setups, making sure conformity with task specifications. In-process assessments involve keeping an eye on welding techniques and criteria, such as warm input and take a trip rate, to avoid issues from happening. This stage enables real-time modifications to welding practices.
Post-weld examinations consist of non-destructive screening (NDT) techniques like radiography, ultrasonic testing, and magnetic bit testing. These methods aid detect inner and surface area problems that could compromise the pipeline's capability. Documentation of all assessment tasks is vital, providing a traceable document that supports conformity with sector criteria.
Educating and qualification of evaluation workers even more enhance the efficiency of these procedures. By adhering to an organized examination method, companies can minimize risks, make certain compliance, and inevitably deliver pipelines that satisfy stringent safety and security and efficiency requirements.
Common Difficulties and Solutions
Pipe welding evaluation presents several usual obstacles that can influence the quality and safety of the final item. One substantial difficulty is the variability in welding methods and materials, which can result in irregular weld high quality. To resolve this, it is essential to establish standardized treatments and training for welders, guaranteeing an uniform strategy throughout projects.
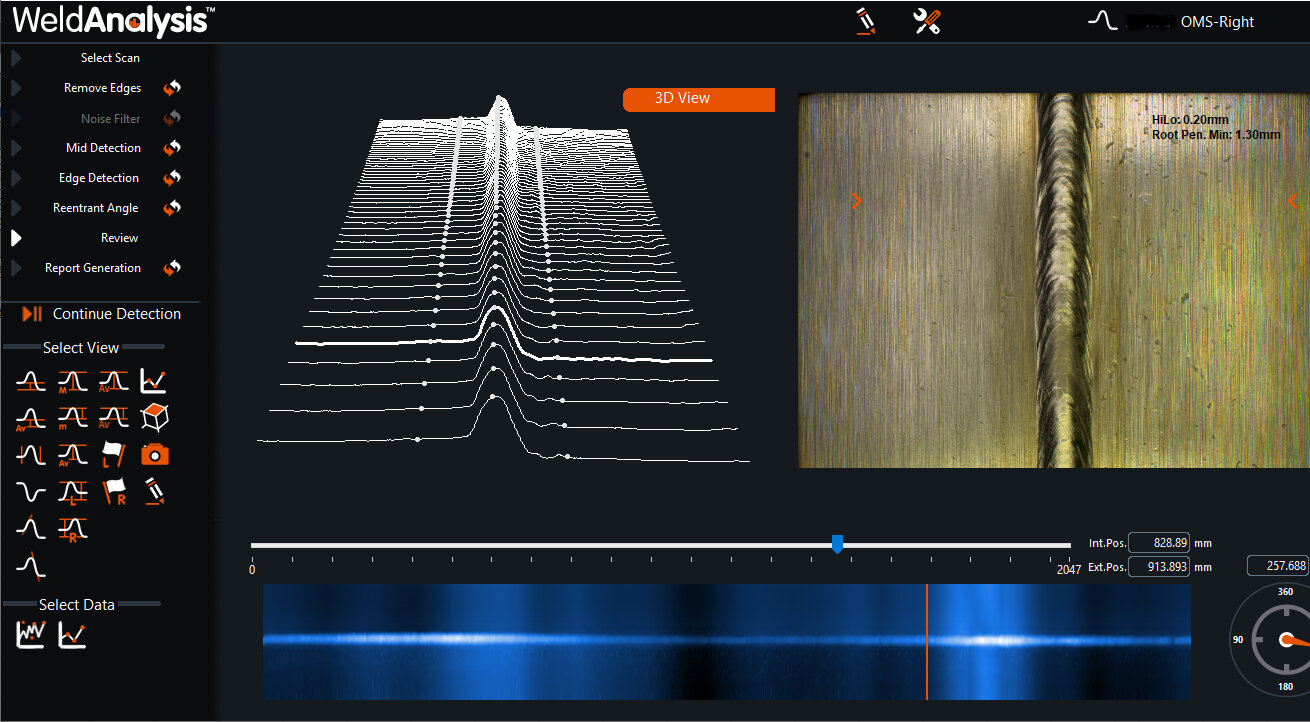
Environmental factors, consisting of temperature level and humidity, can additionally affect the welding process, potentially bring about fractures or insufficient combination. Applying controlled atmospheres and sticking to pre-weld treatments can alleviate these dangers.
Verdict
To conclude, the implementation of ideal techniques for pipe welding inspection is essential for ensuring quality control and compliance additional resources with sector standards. A thorough approach, including different methods such as aesthetic, ultrasonic, and radiographic screening, helps with the recognition of problems throughout all phases of the welding process. Pipeline Welding Inspection. Adherence to established laws and reliable evaluation treatments not only enhances the integrity and safety of pipe systems but additionally mitigates threats connected with welding problems, thus promoting overall operational stability
Compliance with market criteria and laws is important for guaranteeing the quality and security her latest blog of pipeline welding examinations. These requirements give a structure for finest methods in welding processes, products, and assessment techniques, allowing organizations to minimize flaws and boost the stability of pipe systems.In the United States, regulations from the Pipeline and Hazardous Products Safety And Security Administration (PHMSA) govern the security of pipe procedures, mandating rigorous inspection protocols. A methodical approach to inspection incorporates several crucial stages, consisting of pre-weld, in-process, and post-weld evaluations.In final thought, the application of ideal methods for pipe welding evaluation is essential for making certain quality assurance and conformity with market standards.
Report this page